Maximizing your Bottom Line with Ergonomics.
Written by: Kim Moull, Ergonomic Consultant
When you think about the word “Ergonomics” where does your mind go? As an industrial manufacturer, you may be quick to associate ergonomics with concepts such as safety, prevention, and cost savings that go along with these initiatives. The positive impact that ergonomics has on employee health and wellbeing also results in reduced costs for you by preventing lost-time and restricted-work injuries, and potential rehabilitation costs. Sure enough, ergonomics is widely accepted as a crucial component of a well-rounded industrial health and safety program, but how can it also help your company hit its non-safety-related targets?
If speed and productivity are key goals within your internal systems, you aim to eliminate wasted work as much as possible. Excess motion can be a large contributor to wasted work. Through the lens of an Ergonomist, unnecessary motion can be identified and corrected to not only reduce potential burden on your employee, but to also decrease the amount of time required to complete a task. Reducing the motion required for a task can also decrease employee fatigue, which can result in boosted morale and individual productivity. Recently, Options Incorporated assisted a manufacturing client with ergonomic improvements to enhance process efficiencies in their manual materials handling department. The following is an example of one improvement this project included.
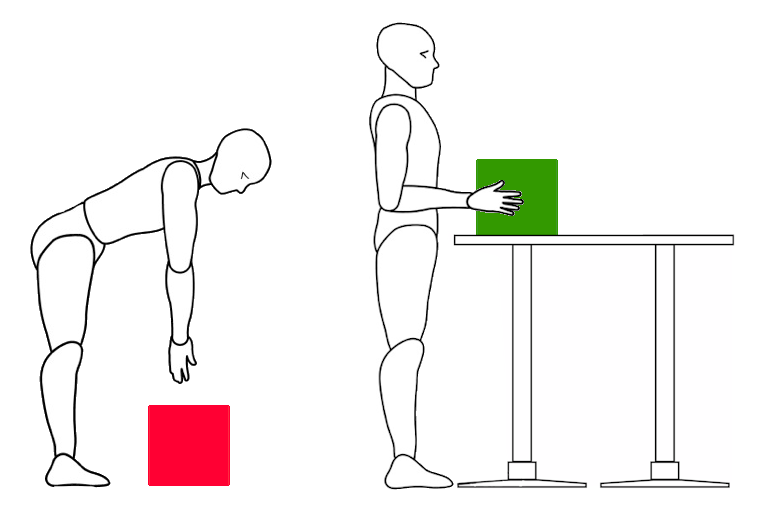
Scenario: An employee lifts a load from the floor once per minute over an 8 hour day and it takes 2 seconds to complete each lift.
Improvement: The Ergonomist knows that lifting from waist-height is not only lower ergonomic risk, but can also reduce the time to complete the task. The process is changed and the lift, from waist-height, now only takes 1 second to complete, saving 40 minutes of time per week.
Rework is another common speed-killer in manufacturing. Since you hold quality to the highest standards, you may occasionally identify post-production flaws in products that must be corrected before sending it to your customer. Identifying part-fit as a root cause of rework is one way that using ergonomics can help address product quality. Parts that do not fit together optimally may not only require high forces to assemble, but can also result in incomplete assembly. Employees may also resort to forcing parts together causing system damage if there is a part-fit issue. The Ergonomist can identify part-fit issues to reduce the forces that your employees are exposed to, improving product quality, and limiting the amount of rework required later.
If your internal systems have competing safety, productivity, and quality targets, ergonomics can be used to help optimize and quantify improvements with the purpose of reaching each of these goals. Even when the dynamic nature of your systems results in a “must-do” situation, when the change has a critical or positive effect on one of your targets, integration of ergonomics can help minimize negative impacts to your other priorities.
Are you intrigued by how the combination of ergonomic principles and lean ideas can provide reductions on work-related ergonomic risks and injuries as well as increase quality and productivity? At Options Inc, we have proven success at integrating ergonomic principles with corporate system targets to help make your workplace more efficient and ergonomically friendly. Contact us to discuss how we can help integrate ergonomics into your existing systems to help meet your targets and maximize your investment.
Contact Us Back to Articles